
UV coating is part of UV printing technology and is considered as one of the most advanced printing technologies in the world.
UV printers may be used on a wide variety of materials and substrates.
These materials include Perspex, plastics, wood, glass, tiles, metals, paper, cardboard, Dibond, and Correx.
Regarding usage, consider bottles of glass, phone covers, golf balls, pens and pencils, key rings, and cards made of plastic, such as cards for memberships.
UV flatbed printers have many advantages over traditional printing processes due to their direct-to-substrate, no-plate manufacturing inkjet printing technology.
We are aware that UV flatbed printers can print on practically any flat material.
Some unusual materials require coating before UV ink printing to improve ink adhesion to their surface.
The question is, which materials should be UV-coated?
Do you require UV coating for your glass, wood, metal, or other materials?
What is UV Coating?
The UV coating fluid consists of specially modified resin and refined auxiliary materials for use in special polymer materials.
Its primary function is to improve the adhesion of UV printing to a pattern on a variety of materials, including glass, tile, metal, melamine board, nylon, PET, PVC, PC, ABS, and stone.
Its qualities include high water resistance, quick drying, and minimal odor.
Classification of UV coatings for printers
There are 6 types of UV printer coatings that are commonly found on the market:
Glass coating
Without the proper preparation, the ultra-smooth, non-porous, and somewhat reflective surface of glass can be difficult to work with, but the end result is well worth the effort.
Suitable for materials such as plexiglass, tempered glass, glazed tiles, crystal and other glasses that require special treatment.
Two types of coating are available, one dries quickly and does not require baking.
The other requires baking in an oven before printing.
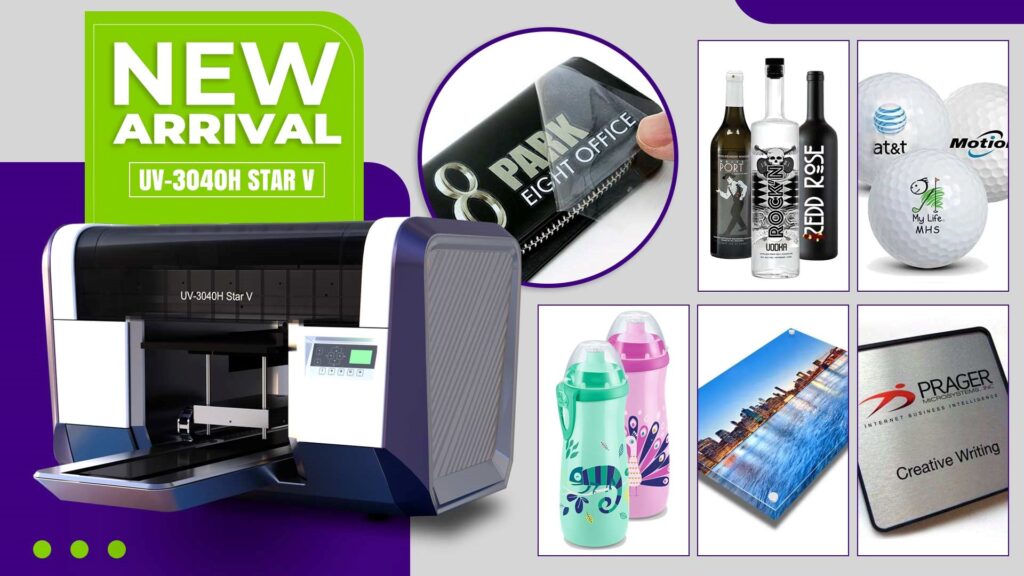
UV coating for PC printer
Today, polycarbonate is frequently used in construction, the fabrication of translucent structures, and architectural embellishment.
Cellular polycarbonate with UV protection is the most preferred material among all available options.
Certain hard PC (Polycarbonate) materials have poor adhesion.
Also some PC materials can be printed directly without coating.
Metal coating
Metal can have a variety of textured surfaces, such as brushed, anodized, or coated, allowing for a wide range of finishes.
However, some brighter and shinier metals, like stainless steel, can be quite difficult to print on and require some setup to get just right.
The metal coating is ideal for aluminum, copper plate, white sheet metal, aluminum alloys and other materials.
Must be applied to the finished product.
It cannot be applied before stamping or injection molding, as this will significantly reduce the effect.
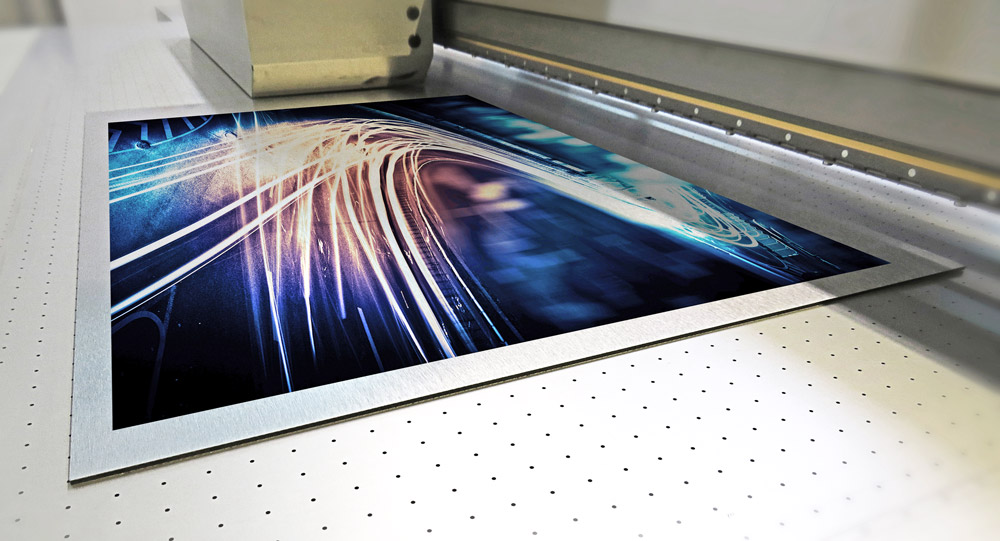
Leather coating
Personalized leather products are constantly in demand and extremely profitable, and UV printing is a quick, cost-effective, and flexible technique of customization.
The leather coating is suited for a variety of leathers, including PVC and PU.
ABS coating
ABS plastic is a popular and adaptable material for UV printing.
It has numerous features and characteristics that make it useful for a variety of applications, including:
- It’s durable, resistant to impact, and resistant to heat.
- Its smooth surface guarantees consistent ink spread and adherence.
- It is widely utilized in the production of toys, automobile parts, electronic devices, and other products.
However, before you begin UV printing on ABS plastic or any other material, make sure it is adequately prepared.
- Clean the surface of the ABS plastic with alcohol and a lint-free cloth.
This will remove any dirt, debris, grease, or fingerprints that could degrade print quality.
- Dry the surface of the ABS plastic.
This ensures that moisture and humidity do not interfere with the curing process.
- Spray primer (UV coating) onto the surface of the ABS plastic. This improves the adherence and endurance of the ink.
Silicone coating
Suitable for rubber and silicone materials.
Weak surface activity requires flame treatment, without it, the adhesion would not be sufficient.
Precautions to be taken when using UV coating
(1) UV coating materials should be of reliable quality and should be obtained from the original equipment manufacturer after extensive testing.
(2) Use different UV coatings for different materials – do not mix them.
(3) In the case when the temperature is low and the air is humid, the UV coating must be applied and left in place for some time before the effect becomes better.
This is after it has had time to dry.
(4) The curing agent should be added to the UV coating according to the required amount before use.
If too much is added at once, the coating will dry quickly and will result in poor quality of the final print.
(5) Since the UV coating is flammable, keep it away from the fire.
(6) If UV coating accidentally gets into your eyes, rinse them quickly with water and seek medical attention immediately.

How to use UV coating to get the best results
Uniform Spraying of UV Coating – The product must have a “uniform” coating application,that is, not just certain areas to be sprayed with the coating and other areas to be left blank.
Application thickness – Be careful when applying the coating, the thickness of the UV coating should not be too thick or too thin.
If the layer is too thin, it will have no effect, while too thick will reduce the adhesion of the UV coating on the sample to which it is applied.
Wait for the UV coating to dry – For optimal results, wait until the coating is completely dry before starting to print after it has been fully sprayed on the surface.
Formulation ratio must change in real time – The coating formulation ratio is not static and must be adjusted according to changes in humidity and temperature over time.
Tips for better use
– The UV coating solution should be kept in a cool, well-lit place.
After each use before storage, it must be closed as soon as possible.
– Use alcohol and a dust-free cloth to wipe the product’s surface before printing.
Then, using the same cloth, wipe the coating evenly over the material, paying particular attention to the edges surrounding the material.
– To avoid evaporation of liquid components of the coating, avoid opening the cap of the liquid coating container for an extended period of time and avoid allowing the coating to come into contact with air.
As the coating dosage will vary for some special materials, it is advised to prepare a small sample in advance to check adhesion (color fastness) before mass printing production.