The application of plastics in the industry has been very diverse for many years.
The most important part of this application relates to the elements made by injection molding.
The increasing use of plastics requires greater commitment from engineers, both in terms of structural precision and tool size.

The mold is one of the most influential factors affecting the formation of the melt in the product with the desired dimensions, achieving a homogeneous structure and surface quality.
Therefore, proper mold construction is a very responsible task for the constructor.
It consists of solving a series of problems caused by rheological and thermodynamic processing processes, the properties of the polymer melt, the optimal geometry performance, operating conditions and mold production processes.
From the viewpoint of rheology and mold geometry problems are set to achieve the desired geometry and surface quality of molded part.
Problems of thermodynamic significance are related to the achievement of the optimum melting temperature in the mold and the realization of proper heat exchange.
At operating conditions, care must be taken to ensure easy installation and disassembly, good sealing of the mold surfaces and the injection molding joint, quick and easy separation.
Under the method of manufacture involves the selection of materials and appropriate processing of the mold, and determining the cost price.
It is obvious that before the constructor raises a number of problems to needs to be solved.
As it is usually not possible to meet all set requirements, designing a mold is a process of finding the optimal variant.
Factors that Influence Plastic Injection Mold Design
A good mold design requires mold designer to have rich knowledge and experience on plastic resin properties, injection molding process, and mold structure and usually there are six typical factors of plastic injection mold design that are important in order to receive best result:
- Mold layout
- Parting line
- Gating system
- Slider & Lifter
- Cooling system
- Ejection system
Plastic injection molding is defined as the process of processing plastics by accelerating the melt into a tool cavity where it is cooled and cured, after which the tool is opened and the molds are removed.
In the processing of polymeric materials, injection molding is by the processed quantities immediately after extrusion.
This technology represents the most important cyclic polymer processing process.
Usually, molding does not require refinement that is, it is a finished product, although in some cases the mold may have refinement, depending on the tool, the complexity of the plastic product, etc.
The short cycle times, the high reproducibility of the quality of the obtained moldings, the high dimensional accuracy and the wide variety of moldings of varying complexity make injection molding technology very popular in plastic processing.
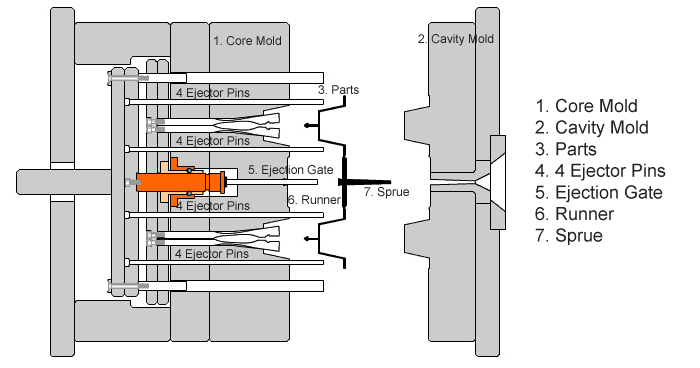
Injection Molding
The most important cyclic procedure for thermoplastic is injection molding.
That is a process of the rapid injection of melt into the tempered mold and its’ solidification into a product.
There is the possibility for automating the process; therefore it is convenient for a great array of products.
The base steps in the injection molding process are:
-mold clamping
-injection
-plastics holding in the mold
-cooling
-mold opening
-product ejection
The process is continuously repeated until a desirable number of products have been produced.
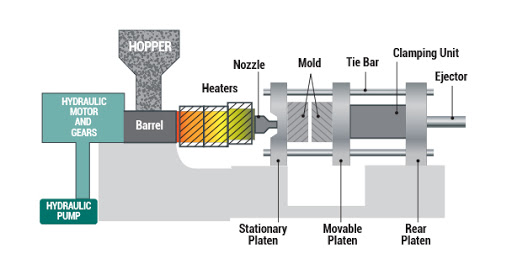
Classification of tools for injection molding
This classification can be made on the basis of several factors:
-Depending on the number of recesses, tools with one or more recesses are distinguished, whereby the same or different parts can be made
-According to the degree of mechanization, they can be with manual ejection, semi-automatic and fully automatic cycle execution.
-Depending on the configuration of the part, it can be tools for simple shapes, parts with outer outlets and parts with outer and inner outlets and threaded parts.
Main advantages:
- parts of very different geometry, dimensions,
degrees of complexity, characteristics can be made - large selection and continuous development of
new materials with different characteristics - material savings
- high degree of automation and short production
time - high accuracy of dimensions and shape of the
finished product - high repeatability
- a small work space to house equipment
- wide scope for refinement, surface treatment and
finishing - production of products in combination with metal
and other materials - injection of multiple components simultaneously
(two-component, three-component, four-component)
The main disadvantages
-high cost of basic equipment
-complex thermodynamic-rheological process
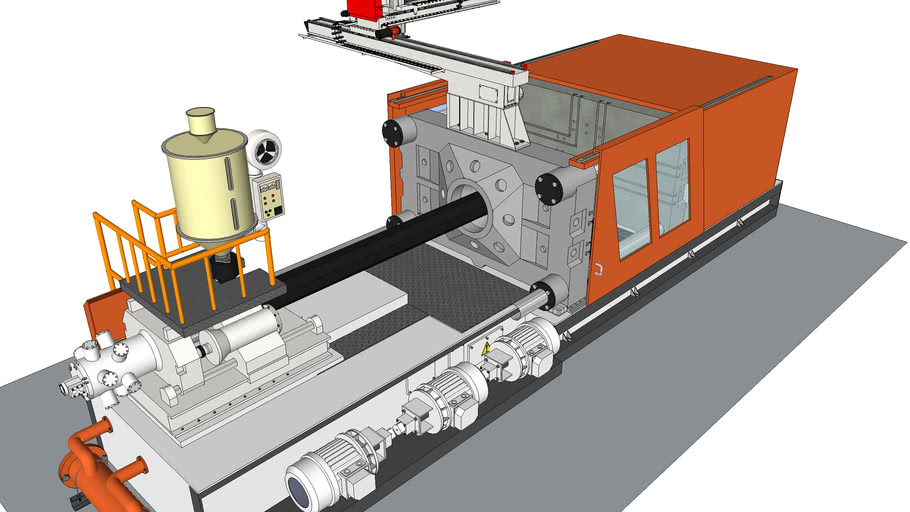
Plastics have been used a lot in recent years, so there is no industry where they have not found the application.
They have a major involvement in the following areas:
-telecommunication equipment,
-electronic equipment,
-car industry,
-children’s toys,
-computers and computer components, etc.
The level of required quality and precision of plastic parts production is constantly increasing as well as other market demands.
So mistakes and problems in planning, design, production and control are less and less tolerated.
That is why a good mold designing in the beginning of this process is one of the very important factors in order to receive final result with satisfying qualities.